Exploring Cemented Carbide and Its Significance
Definition and Composition of Cemented Carbide
Cemented carbide, also known as hard metal, is a composite material frequently favored for its exceptional hardness and durability. It is composed of finely powdered carbide particles, bound together by a metallic binder, typically cobalt. The primary component of cemented carbide is tungsten carbide (WC), known for its resilience and ability to maintain sharp edges even under extreme conditions. This unique composition makes cemented carbide an essential material in various industrial applications, particularly for cutting tools.
Strategic Importance of Tungsten in Cemented Carbide
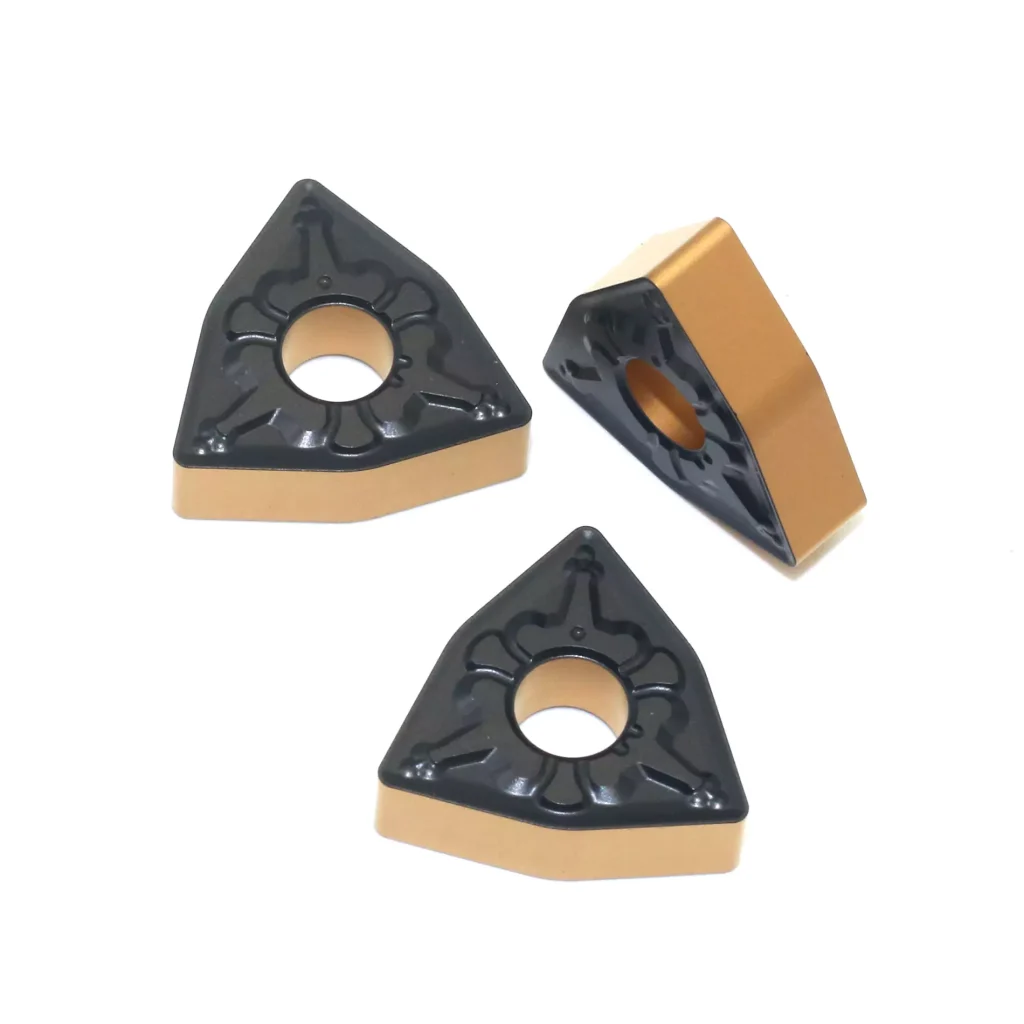
Tungsten, the primary element in tungsten carbide, plays a critical role in determining the properties of cemented carbide. It provides unmatched wear resistance and the robustness necessary for cutting and drilling applications. Tungsten’s high melting point and stiffness make it the ideal element for forming hard metal composites. However, tungsten’s strategic importance extends beyond its material properties. The metal is considered crucial for national security, technological advancements, and economic growth, making its supply and availability a matter of significant interest and concern.
Price Fluctuations and Supply Challenges
The global tungsten market has experienced notable price fluctuations due to various factors, such as geopolitical tensions, mining regulations, and supply-demand imbalances. For instance, China, the largest producer of tungsten, has exerted considerable influence on global prices through export restrictions and quota implementations. These supply challenges have created volatility in the market, affecting the cost and availability of cemented carbide. Consequently, industries reliant on carbide inserts must navigate these fluctuations and seek alternatives or adjustments in their procurement strategies.
Unveiling the Development of Coated Inserts
Motivation Behind Coating Cemented Carbide Inserts
Coating cemented carbide inserts emerged as a solution to enhance their performance and longevity. The motivation behind this innovation was to address the limitations of uncoated carbide tools, such as rapid wear and susceptibility to heat. Coating technologies provide an additional layer of protection, significantly improving the tool’s lifespan and cutting efficiency. Coated inserts can withstand higher temperatures and reduce the friction between the tool and workpiece, ensuring better performance in demanding applications.
Benefits Associated with Coated Inserts
The benefits of using coated carbide inserts are manifold. One of the primary advantages is improved wear resistance, resulting in longer tool life and reduced frequency of tool changes. Coated inserts also offer superior heat resistance, enabling higher cutting speeds and feeds without compromising tool integrity. Furthermore, the coating enhances the tool’s ability to cut through hard materials with precision, reducing the occurrence of tool breakage and ensuring consistent quality in the finished workpiece. These benefits collectively contribute to increased productivity and cost-efficiency in manufacturing processes.
Applications in High-Speed and High-Feed Cutting
Coated carbide inserts are particularly valuable in high-speed and high-feed cutting applications, which demand exceptional tool performance and resilience. The coatings enable the inserts to endure the extreme conditions encountered during high-speed machining, including elevated temperatures and intense mechanical stresses. This capability is crucial for industries such as aerospace, automotive, and metalworking, where precision and efficiency are paramount. The use of coated inserts in these applications results in faster machining times, improved surface finishes, and reduced wear, thereby enhancing the overall quality and productivity of the manufacturing process.
Historical Perspective and Technological Innovations
Focus on Technological Advancements and Future Trends
The evolution of coating technologies for carbide inserts has been marked by significant technological advancements and continuous improvements. Understanding this historical perspective provides valuable insights into the innovations that have shaped the industry. Starting from simple thermal coatings to advanced chemical and physical vapor deposition methods, the journey of coated inserts reflects a commitment to enhancing tool performance. Future trends indicate a focus on developing more resilient coatings, integrating nanotechnology, and exploring environmentally sustainable coating techniques. These trends promise to drive further advancements, ensuring that carbide inserts continue to meet the ever-evolving demands of modern manufacturing.
Vapor Deposition Coating Technology for Cutting Inserts
Overview of Manufacturing Methods and Features
Explanation of Manufacturing Methods
The manufacturing methods for coating carbide inserts involve complex processes designed to achieve optimal coating thickness and adhesion. These methods include chemical vapor deposition (CVD) and physical vapor deposition (PVD), each offering unique benefits and applications. The choice of method depends on the desired properties of the coated insert, such as hardness, wear resistance, and thermal stability. Understanding these methods is crucial for selecting the appropriate coating technology for specific industrial needs.
Chemical Vapor Deposition (CVD) Technology
CVD technology involves the chemical reaction of vapor-phase precursors on the surface of the carbide insert, forming a thin, uniform coating. This method is favored for its ability to produce coatings with excellent adhesion and uniform thickness, making it ideal for applications requiring high wear resistance and durability. CVD coatings are typically used for high-temperature applications, where the coating’s ability to withstand intense heat is paramount.
Physical Vapor Deposition (PVD) Technology
PVD technology, on the other hand, involves the physical transfer of material from a source to the surface of the carbide insert through vaporization. This method allows for precise control over coating thickness and composition, resulting in superior surface finishes and hardness. PVD coatings are highly versatile, making them suitable for a wide range of applications, including those requiring enhanced cutting performance and reduced friction.
Environmental Impact of Dry Film-Forming Processes
An important consideration in the development of coating technologies is their environmental impact. Both CVD and PVD methods offer dry film-forming processes that reduce the need for liquid coolants and lubricants, thereby minimizing waste and environmental pollution. This environmentally friendly approach aligns with the growing demand for sustainable manufacturing practices and highlights the industry’s commitment to reducing its ecological footprint.
Wear Mechanisms in Coated Inserts
Characteristics of Coated Films
The characteristics of coated films on carbide inserts determine their effectiveness in various industrial applications. Coated films are engineered to possess high hardness, toughness, and resistance to wear, which are essential for cutting and machining tasks. These properties ensure that the coated inserts maintain their cutting edges for extended periods, even under harsh operating conditions. Additionally, coated films are designed to be chemically inert, preventing reactions with workpiece materials that could degrade the tool’s performance.
Resistance to Wear and Oxidation
One of the primary objectives of coating technologies is to enhance the resistance of carbide inserts to wear and oxidation. Wear resistance is crucial for prolonging the tool’s lifespan and maintaining its cutting efficiency. Advanced coatings, such as those applied through CVD and PVD methods, provide a protective barrier that minimizes the tool’s exposure to abrasive forces and chemical reactions. This resistance to wear and oxidation results in more consistent performance and reduces the need for frequent tool changes, thereby increasing productivity.
Effectiveness of Thin Films in Reducing Wear
Thin films play a vital role in reducing wear on carbide inserts by providing a low-friction surface that minimizes contact between the tool and workpiece. These films are meticulously engineered to achieve the optimal balance between thickness and adherence, ensuring sufficient protection without compromising the tool’s cutting capabilities. The effectiveness of thin films in reducing wear is evident in various high-performance applications, where precision and longevity are paramount. By minimizing wear, thin films contribute to more efficient machining processes and lower operational costs.
Breakthroughs in CVD Coating Technology
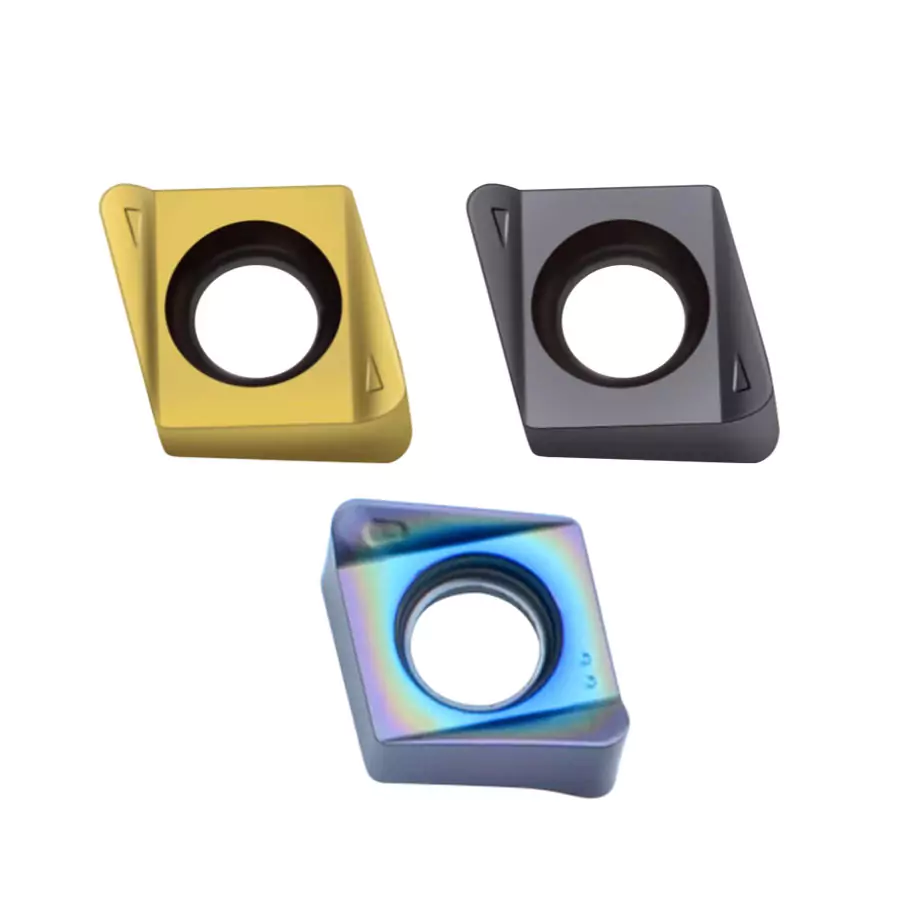
Development of Carbide Substrates for CVD Coating
Historical Background
The development of carbide substrates for CVD coating has a rich historical background, marked by continuous research and innovation. Initially, the focus was on identifying suitable materials and processes that could withstand the high temperatures and chemical reactions involved in CVD. Over time, advancements in material science and engineering have led to the creation of carbide substrates that offer superior wear resistance and thermal stability. This historical progression underscores the significance of ongoing research in enhancing the performance of coated carbide inserts.
Advances in Zirconium-Doped Substrates
One notable advancement in CVD coating technology is the use of zirconium-doped substrates. The incorporation of zirconium into carbide substrates enhances their mechanical properties, including toughness and hardness. Zirconium-doped substrates exhibit improved resistance to wear and oxidation, making them ideal for demanding cutting applications. The development of these advanced substrates represents a significant milestone in the evolution of CVD coatings, offering enhanced performance and durability.
Advancements in CVD Coating Technology
Evolution of Titanium-Based Coatings
Titanium-based coatings have undergone significant evolution in CVD technology, resulting in remarkable improvements in tool performance. Initially, simple titanium nitride (TiN) coatings were used to enhance wear resistance. However, advancements have led to the development of more complex titanium-based coatings, such as titanium carbonitride (TiCN) and titanium aluminum nitride (TiAlN). These coatings offer superior hardness and thermal stability, making them suitable for a wide range of cutting applications. The continuous evolution of titanium-based coatings highlights the industry’s commitment to innovation and excellence.
Progress in Alumina Coatings
Alumina (Al2O3) coatings have also seen substantial progress in CVD technology. Alumina coatings are prized for their high hardness, wear resistance, and thermal stability. They are particularly effective in applications involving high-temperature machining, where maintaining tool integrity is crucial. Recent advancements have focused on refining the deposition processes to achieve uniform and defect-free alumina coatings, enhancing their performance and longevity. The progress in alumina coatings underscores the importance of continuous research and development in coating technologies.
Introduction of Super FF Coat
The introduction of the Super FF Coat represents a groundbreaking achievement in CVD coating technology. This innovative coating combines the benefits of multiple advanced materials, resulting in exceptional hardness, toughness, and thermal stability. The Super FF Coat is designed to withstand the most demanding cutting conditions, offering unparalleled performance and longevity. Its development reflects the industry’s dedication to pushing the boundaries of coating technology and delivering superior solutions for modern manufacturing challenges.
Innovation in Post-Coating Surface Treatment Techniques
Importance of Surface Smoothing
Post-coating surface treatment techniques play a crucial role in enhancing the performance of coated inserts. One important aspect of these treatments is surface smoothing, which aims to reduce surface roughness and improve the tool’s cutting efficiency. Smooth surfaces minimize friction and heat generation during machining, leading to improved tool life and better surface finishes on the workpiece. The importance of surface smoothing cannot be overstated, as it directly impacts the overall performance and longevity of coated inserts.
Techniques for Surface Stress Control
In addition to surface smoothing, techniques for surface stress control are vital for optimizing the performance of coated inserts. Residual stresses can adversely affect the tool’s durability and cutting performance. Advanced post-coating treatments, such as peening and annealing, are employed to control and mitigate surface stresses. These techniques enhance the mechanical properties of the coated surface, ensuring that the insert maintains its integrity and performance under challenging operating conditions. The innovation in surface stress control techniques underscores the industry’s commitment to delivering high-performance cutting tools.
Pioneering Advances in PVD Coating Technology
Super Nanomultilayer Coating Technology Breakthroughs
Development of TiN and TiAlN Coatings
The development of titanium nitride (TiN) and titanium aluminum nitride (TiAlN) coatings represents significant breakthroughs in PVD coating technology. TiN coatings are known for their excellent hardness and wear resistance, while TiAlN coatings offer enhanced thermal stability and oxidation resistance. These coatings have become staples in the manufacturing industry, enabling high-speed and high-performance cutting applications. The continuous innovation in TiN and TiAlN coatings reflects the ongoing pursuit of excellence in PVD technology.
Introduction of ZX Coat and Super ZX Coat
The introduction of the ZX Coat and Super ZX Coat marks a new era in PVD coating technology. These advanced coatings are designed to offer superior hardness, toughness, and thermal stability. The ZX Coat features a unique multilayer structure that enhances its wear resistance and cutting performance. The Super ZX Coat, an evolution of the ZX Coat, incorporates additional advanced materials to further improve its durability and performance. These coatings are ideal for demanding applications, providing exceptional tool life and cutting efficiency.
Advances in AlTiSiN-Based Coatings
Aluminum titanium silicon nitride (AlTiSiN) coatings represent another significant advancement in PVD technology. AlTiSiN coatings offer a unique combination of hardness, thermal stability, and oxidation resistance. They are particularly effective in high-speed and high-temperature cutting applications, where maintaining tool performance is critical. Advances in AlTiSiN-based coatings have focused on optimizing their composition and deposition processes, resulting in coatings that deliver superior performance and longevity. The progress in AlTiSiN coatings underscores the industry’s dedication to innovation and excellence.
Enhancing Tribological Properties with Lubricious Coating
Diamond-Like Carbon (DLC) Characteristics
Diamond-like carbon (DLC) coatings are renowned for their exceptional tribological properties, including high hardness, low friction, and excellent wear resistance. DLC coatings are used to enhance the performance of carbide inserts in applications where low friction and high durability are essential. The unique characteristics of DLC coatings make them ideal for reducing wear and extending tool life, particularly in high-speed and high-precision cutting operations.
Development of Aurora Coat and Brilliant Coat
The development of the Aurora Coat and Brilliant Coat represents significant advancements in lubricious coating technology. These coatings are engineered to provide exceptional hardness, low friction, and enhanced wear resistance. The Aurora Coat features a multilayer structure that optimizes its tribological properties, making it ideal for high-performance cutting applications. The Brilliant Coat, an evolution of the Aurora Coat, incorporates additional advanced materials to further enhance its performance. These coatings offer unparalleled tool life and cutting efficiency, reflecting the industry’s commitment to delivering cutting-edge solutions.
Importance of Low Friction and Lubricity
The importance of low friction and lubricity in coated inserts cannot be overstated. These properties are crucial for minimizing wear, reducing heat generation, and improving cutting efficiency. Coated inserts with low friction and high lubricity extend tool life, enhance surface finishes, and increase productivity. The development of advanced lubricious coatings, such as DLC, Aurora Coat, and Brilliant Coat, highlights the industry’s focus on optimizing tribological properties to meet the demands of modern manufacturing processes.
Future Developments
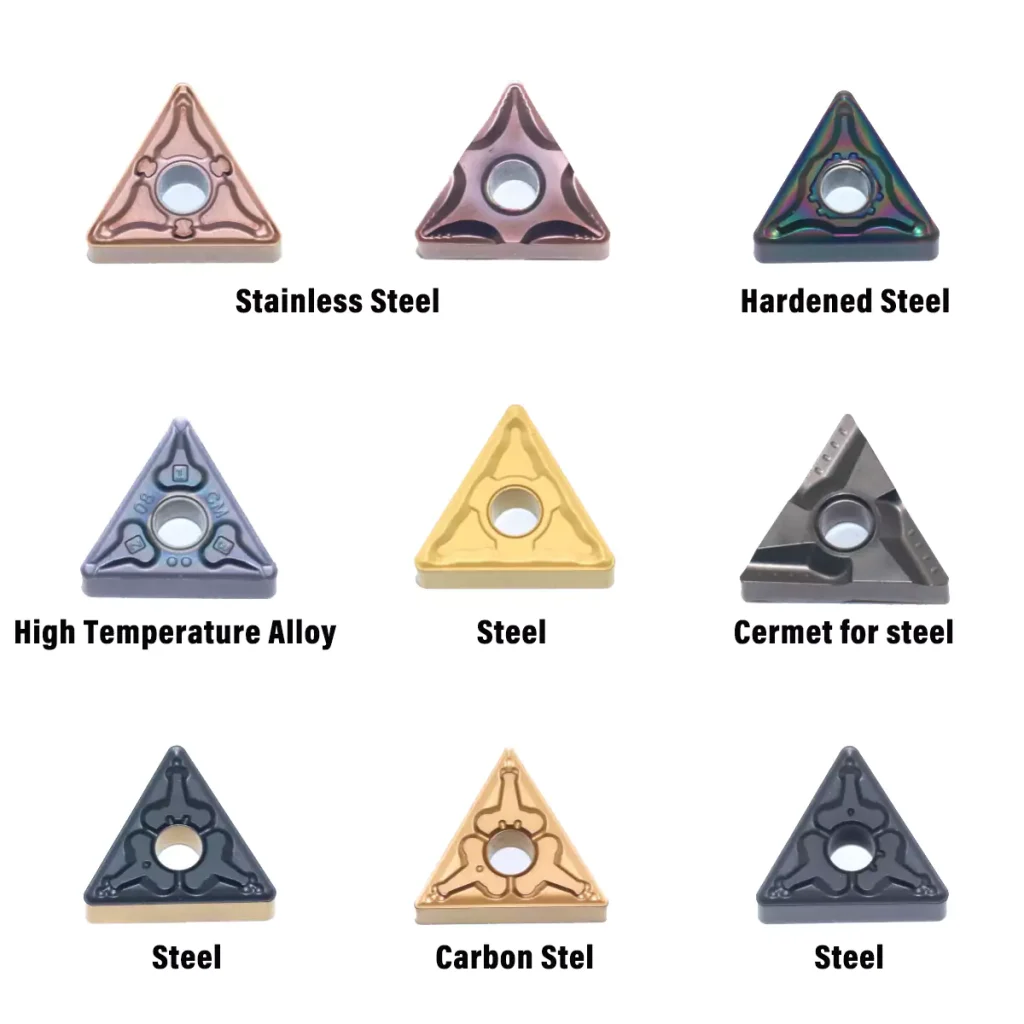
Prospects for CVD Coatings
Ongoing Research in Crystal Orientation and Microstructure
The future prospects for CVD coatings are promising, with ongoing research focusing on optimizing crystal orientation and microstructure. These factors significantly impact the coating’s hardness, toughness, and wear resistance. Advances in understanding and controlling crystal orientation and microstructure will lead to the development of superior CVD coatings with enhanced performance and durability. The continuous research in this area underscores the industry’s commitment to innovation and excellence.
Potential New Materials for Coatings
The exploration of potential new materials for CVD coatings is another exciting area of future development. Researchers are investigating novel materials that offer unique combinations of hardness, toughness, and thermal stability. These new materials have the potential to revolutionize CVD coating technology, providing unprecedented performance and durability. The development of new materials reflects the industry’s determination to push the boundaries of coating technology and deliver superior solutions for modern manufacturing challenges.
Prospects for PVD Coatings
Research on Nanocrystal-Amorphous Structures
The future prospects for PVD coatings are equally promising, with research focusing on nanocrystal-amorphous structures. These structures offer unique mechanical and tribological properties, including enhanced hardness, toughness, and wear resistance. Advances in understanding and optimizing nanocrystal-amorphous structures will lead to the development of superior PVD coatings with exceptional performance and durability. The continuous research in this area highlights the industry’s dedication to innovation and excellence.
Expectations for Novel Developments in Coatings
The expectations for novel developments in PVD coatings are high, with researchers exploring a wide range of advanced materials and deposition techniques. These developments aim to deliver coatings with unprecedented performance and durability, meeting the ever-evolving demands of modern manufacturing processes. The ongoing pursuit of novel developments reflects the industry’s commitment to pushing the boundaries of coating technology and delivering cutting-edge solutions for the future.
In conclusion, the evolution of carbide inserts coating technologies has been marked by significant advancements and continuous improvements. The development of CVD and PVD coatings, along with breakthroughs in post-coating surface treatment techniques, has revolutionized the performance and durability of carbide inserts. Ongoing research and innovation promise to drive further advancements, ensuring that carbide inserts continue to meet the demands of modern manufacturing processes. The future of coating technologies is bright, with exciting prospects for new materials, optimized structures, and environmentally sustainable practices.