Understanding Material Hardness Tests
Overview of Material Hardness Tests
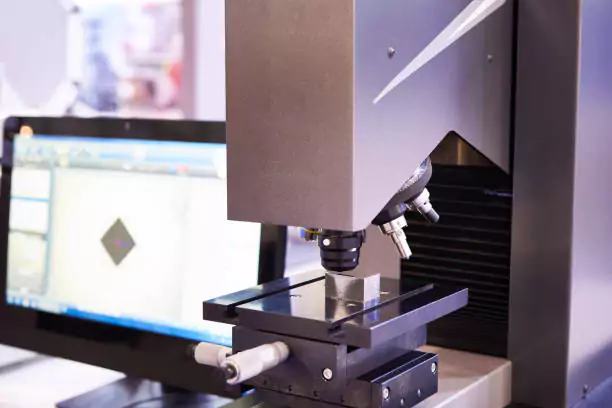
Material hardness is an essential attribute in engineering and industrial applications, as it dictates how a material endures wear, deformation, and indentation. There are various tests designed to measure hardness, each utilizing distinct methods and producing different outcomes.
Vickers Hardness Test
The Vickers Hardness Test employs a diamond-shaped indenter pressed into the material under a specific load. The test measures the diagonal length of the resultant indentation, converting it into a hardness value. This method is applicable across a spectrum of materials, from softer metals to harder alloys and ceramics. Its versatility and accuracy make it widely used in research and quality control.
Rockwell Hardness Test
The Rockwell Hardness Test utilizes a ball or cone-shaped indenter and applies a standard load to create an indentation. The depth of this indentation determines the hardness value. This test is popular due to its simplicity and rapid results, making it suitable for production environments where quick hardness assessment is essential. The Rockwell test is particularly useful for metals and is frequently used in the automotive and aerospace industries.
Brinell Hardness Test
The Brinell Hardness Test involves pressing a hard steel or carbide ball into the material under a specified load. The diameter of the indentation left on the material’s surface correlates with its hardness. This method is favored for testing materials with non-uniform or coarse grain structures, such as cast iron and forged metals. Despite being slower than other methods, it provides reliable results for large and coarse components.
Purpose of Hardness Testing
Hardness testing plays a crucial role in material science and engineering by helping to determine the wear resistance and durability of materials under various conditions. It offers valuable insights into how materials behave when subjected to stress, aiding in the design and selection of appropriate materials for specific applications. Additionally, hardness tests are vital for quality control during manufacturing processes, as they help identify any material inconsistencies that could impact performance.
Question of Accuracy
The accuracy of a Hardness Tester Scale is influenced by the specific method and its application to the material in question. Variations in preparation, indentation, and measurement techniques play crucial roles. While each hardness test has its advantages, understanding the nuances of each method is necessary to ensure precise and reliable results.
Exploring Material Hardness
Definition of Material Hardness
Material hardness can be defined as the resistance of a material to deformation, particularly permanent deformation, scratching, cutting, or abrasion. It is a key property that indicates how well a material can withstand mechanical forces without significant degradation. This makes hardness an important factor in determining the suitability of materials for various industrial and manufacturing purposes.
Factors Affecting Material Hardness
Several factors can affect the hardness of a material, influencing its performance and suitability for specific applications.
Heating
Applying heat can greatly influence a material’s hardness. In numerous metals, heating typically results in decreased hardness because the metal’s structure becomes softer. However, specific heating methods such as tempering can enhance certain mechanical characteristics, like toughness and impact resistance. Consequently, thermal treatments are essential for adjusting material hardness to meet particular requirements.
Hammering
Hammering, or work hardening, increases the hardness of a material by deforming its structure through mechanical forces. This process introduces dislocations and defects within the material’s crystal lattice, enhancing its strength and hardness. Work hardening is commonly used in machining and metalworking to improve the wear resistance and fatigue life of components.
Measurement of Hardness
The measurement of hardness involves assessing how materials respond to applied forces, usually through indentation tests.
Resistance to Indentation
Resistance to indentation is a primary criterion for measuring hardness. In various testing methods, indenters are pressed into the material’s surface under controlled conditions. The size, depth, or shape of the resultant indentation is measured and correlated with hardness values. The different Hardness Tester Scales, such as Vickers, Rockwell, and Brinell, provide specific methodologies to quantify this resistance accurately.
Relationship Between Indentation and Hardness
The correlation between indentation and hardness is straightforward; materials that exhibit smaller and shallower indentations are harder, whereas those with larger and deeper indentations are softer. Accurately interpreting these indentations is crucial for assessing material hardness and understanding its effects on material performance. Different Hardness Tester Scales evaluate these indents in various ways, leading to differences in reported hardness values.
By understanding material hardness tests and their respective scales, industry professionals can select and utilize the most appropriate methods for their specific applications, ensuring accurate and meaningful hardness measurements.
Differentiating Various Hardness Testing Methods
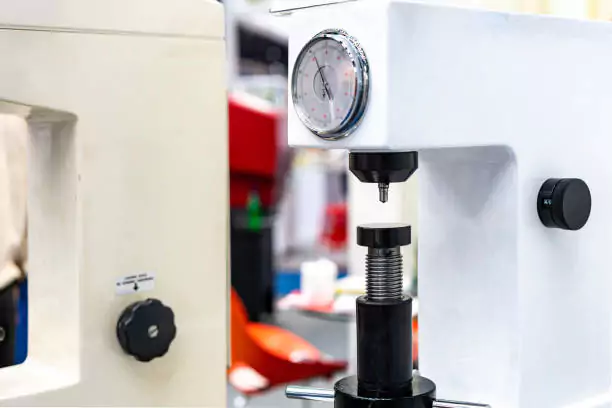
Vickers Hardness Testing
Procedure and Indenter
In the Vickers Hardness Testing method, a diamond-shaped pyramid indenter is used to assess material hardness. The indenter, featuring opposing face angles of 136 degrees, is applied to the material’s surface under a selected load. Once the load is applied, an indentation is created, and the diagonals of this indentation are meticulously measured using a microscope. The hardness value is then calculated by applying a specific formula that takes into account the load and the dimensions of the indentation, ensuring precise measurement and consistency.
Applications and Advantages
This method is versatile, applicable to a wide variety of materials, including metals, ceramics, and composites. Its ability to provide a continuous scale of hardness values enables it to deliver high precision. The Vickers method is especially advantageous for testing thin materials or coatings due to the small indentation size, yielding detailed results. Moreover, it is widely utilized in laboratory settings and quality control processes because of its high accuracy and reliability.
Challenges and Considerations
Despite its advantages, Vickers Hardness Testing can present certain difficulties. The sample surface preparation needs to be executed with great care to prevent inaccuracies in measuring indentations. Moreover, the necessity for a microscope to gauge these indentations can render this method relatively more time-consuming than alternative techniques. Extensive training for operators is essential to properly conduct the test and accurately interpret the results, which can be a drawback in environments requiring high throughput.
Rockwell Hardness Testing
Procedure and Indenter
The Rockwell Hardness Testing method employs either a spherical or cone-shaped indenter, depending on the specific scale being used. The procedure involves pressing the indenter into the material’s surface under an initial minor load, followed by a larger, definitive load. The depth of the indentation created under the larger load is then measured. The hardness value is determined based on the depth of the indentation relative to the indentation made under the initial minor load.
Applications and Advantages
One of the primary advantages of the Rockwell method is its speed and simplicity, making it highly suitable for production and manufacturing settings where quick, repeatable measurements are necessary. It is particularly effective for metals and alloys, finding significant application in the automotive, aerospace, and metalworking industries. This method also offers a straightforward procedure that requires minimal sample preparation and training.
Challenges and Considerations
However, the Rockwell method has its limitations. Variations in material properties, like hardness gradients and surface finish, can sometimes lead to inconsistent results. The depth of indentation can introduce inaccuracies when testing very thin or extremely hard surfaces. To ensure accurate readings, it’s essential that the test is performed on flat and clean sample surfaces, free from any contaminants or irregularities.
Brinell Hardness Testing
Procedure and Indenter
Brinell Hardness Testing employs a spherical indenter, generally made of hardened steel or carbide, which is pressed into the material under substantial load. The diameter of the resulting indentation is then measured, and this measurement is used to determine the Brinell Hardness Number (BHN) by relating the applied load to the indentation area. The accuracy of this method heavily relies on precise measurement of the indentation diameter using a microscope or an optical projector.
Applications and Advantages
This testing method is particularly beneficial for evaluating materials with non-uniform or coarse grain structures, such as cast iron, metals with rough surfaces, and large fabricated components. The large indentation size in Brinell testing effectively averages out variations caused by surface and microstructural inconsistencies, providing reliable and reproducible results. Brinell testing is also versatile, being suitable for a wide range of load and material combinations.
Challenges and Considerations
Brinell Hardness Testing can be relatively slow in comparison to other methods due to the larger indentations required and the need for precise measurement of these indentations. The larger deformation zone can limit its applicability in testing small or thin samples. Preparation of the test material’s surface is critical, as any imperfections can significantly affect the accuracy and consistency of the hardness values obtained. Equipment needs to be maintained precisely to ensure the indenter and applied loads are consistent.
By comprehensively understanding the fundamental procedures, advantages, challenges, and accurate application of the Hardness Tester Scale through methods such as Vickers, Rockwell, and Brinell, professionals in engineering and manufacturing can make informed decisions that guarantee precise hardness testing results for diverse materials and scenarios.
Comparing Accuracy Among Hardness Testing Methods
Accuracy of Vickers Hardness Test
The Vickers Hardness Test is renowned for its exceptional precision and the adaptability of its Hardness Tester Scale. This method involves measuring the diagonal length of an indentation created by a diamond pyramid indenter, enabling its application to a broad spectrum of materials, such as metals, ceramics, and thin coatings. The high accuracy of the Vickers method stems primarily from the microscopic measurement of the indentation. However, achieving this level of accuracy necessitates a well-prepared sample and a skilled operator to maintain consistency. Variations in measurement and sample preparation can lead to errors, but when executed correctly, the Vickers test produces highly reliable results.
Influencing Factors
Several factors influence the accuracy of the Vickers Hardness Test. One critical factor is the condition of the sample surface; it must be smooth and free of contaminants to avoid any distortions in the indentation. The load applied during the test must be carefully controlled and consistent, as variations can affect the results. Additionally, the precision of the microscope used to measure the indentation is vital; higher resolution instruments improve measurement accuracy. Lastly, operator expertise plays a significant role, as proper alignment and pressure application are crucial for obtaining accurate readings.
Accuracy of Rockwell Hardness Test
The Rockwell Hardness Test stands out due to its simplicity and speed, which is advantageous in industrial settings. The test measures the depth of an indentation created by a ball or cone-shaped indenter under a major load, compared to an initial minor load, yielding a direct hardness value. Its Hardness Tester Scale is regularly employed for metals and hard substances, offering quick and repeatable results. While it provides reliable data under ideal conditions, the Rockwell test’s accuracy can be affected by material properties, including surface finish and hardness gradients.
Influencing Factors
The accuracy of the Rockwell Hardness Test is influenced by several factors, such as the uniformity and cleanliness of the sample surface. The presence of scale, coatings, or dirt can skew the depth measurement of the indentation. The correct choice of scale and indenter type must align with the material being tested to ensure accurate results. Variations in operator technique, such as the consistent application of loading and proper maintenance of the testing machine, also significantly impact the measured hardness values. Furthermore, thin or extremely hard surfaces can produce unreliable data if not properly accounted for in the test setup.
Accuracy of Brinell Hardness Test
The Brinell Hardness Test is especially effective for materials with coarse or non-uniform structures. It employs a large spherical indenter along with a substantial load to create an easily measurable indentation, which the Hardness Tester Scale then converts into a hardness value. This method demonstrates greater tolerance for surface imperfections compared to other tests, making it dependable for rough or irregular surfaces. The large indentation size averages out microstructural inconsistencies, thereby improving the reliability of the results. However, this comes at the expense of increased testing time and more intensive sample preparation requirements.
Influencing Factors
Several factors affect the accuracy of the Brinell Hardness Test, starting with the condition of the sample surface. Any imperfections or debris can distort the indentation and lead to inaccuracies. The precision of the indentation diameter measurement is critical, requiring accurate optical equipment and skilled operators. The material’s thickness should be adequate to ensure the load doesn’t cause through-thickness deformations, affecting the precision of the readings. Consistency in the applied load and the calibration of the testing machine also play essential roles in maintaining the reliability of the hardness values.
Suitability of Testing Methods to Materials
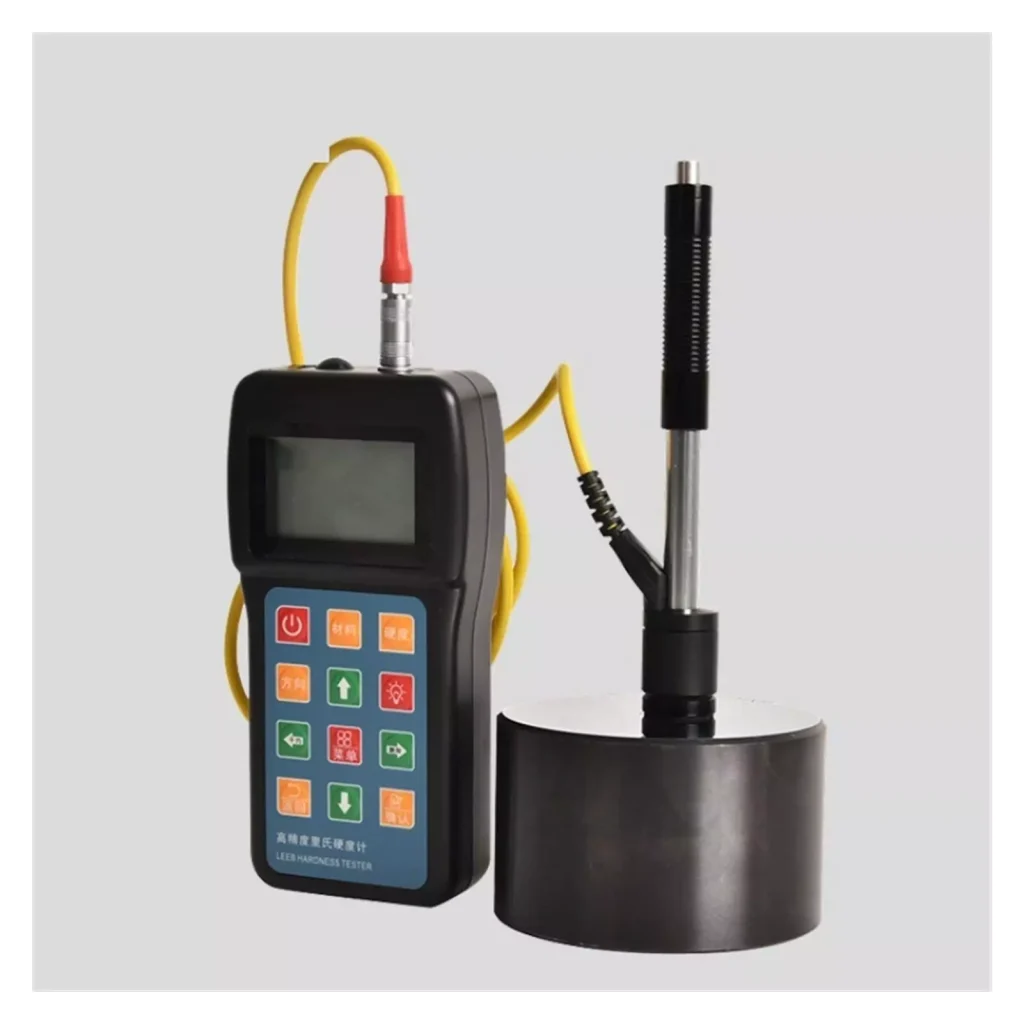
When considering which Hardness Tester Scale to use, it is crucial to align the test method with the material properties to obtain accurate readings. Each hardness test is tailored to specific material characteristics, and choosing the appropriate method enhances the validity of the results.
Material Properties
Different materials possess varying properties that influence their interaction with hardness testers. For instance, hard materials like ceramics and alloys may require the precision of the Vickers test, while tougher, less uniform materials like cast iron are better suited for the Brinell test. The Rockwell test is effective for large-scale industrial applications where metals with consistent surface finishes are tested. Understanding the material’s hardness, grain structure, and surface condition helps in selecting the right test.
Test Method Alignment
Aligning the test method with the material’s properties is crucial for achieving accurate hardness measurements. For example, the Vickers method is excellent for detailed laboratory analysis of fine materials, while the Brinell method is ideal for large, coarse components used in industrial contexts. Rockwell’s quick and straightforward procedure is best suited for metals in high-throughput manufacturing settings. The choice of scale, indenter type, and load must be matched to the specific requirements of the material to ensure reliable and meaningful hardness data.
By evaluating the accuracy and suitability of various hardness testing methods, industry professionals can make informed decisions regarding the most appropriate Hardness Tester Scale for their specific material and application needs. This ensures precision and reliability in material hardness assessments, ultimately leading to improved product quality and performance.
Practical Aspects in Implementing Hardness Tests
Operator Skill and Consistency
The precision of hardness tests largely depends on the skill and consistency of the operator conducting the test. Proper training and experience are essential for operators to accurately interpret the results, calibrate equipment, and handle samples meticulously. Variations in operator technique, such as the speed and angle at which the indenter is applied, can significantly impact the accuracy of the Hardness Tester Scale readings. Consistency in applying the indenting force, timing of the indentation, and precisely measuring the indentation depth or diameter are all crucial for minimizing errors and ensuring reliable results. Continuous training and adherence to standardized testing procedures can greatly enhance the reliability and repeatability of hardness tests.
Sample Preparation and Cleanliness
The condition of the sample being tested plays a critical role in the accuracy of hardness testing. Proper sample preparation involves cleaning the material’s surface to remove any contaminants like oil, dirt, or oxidation that could affect the indentation process. Surface flatness is also vital; uneven or rough surfaces can lead to distorted indentations, causing inaccurate readings on the Hardness Tester Scale. For materials requiring fine measurement, like those assessed by the Vickers or Rockwell methods, achieving a smooth, polished surface is essential. Additionally, maintaining sample integrity—like avoiding any micro-cracking or deformations during preparation—ensures the material properties are represented accurately in the test results.
Test Environment and Conditions
The environmental conditions under which hardness tests are performed can significantly influence the accuracy of the outcomes. Temperature, humidity, and vibration are critical environmental factors that must be controlled to guarantee consistent readings. For example, fluctuations in temperature can cause the material to expand or contract, which affects the indentation size and thus the hardness value. Humidity can lead to surface oxidation, particularly in metals, potentially interfering with test results on the Hardness Tester Scale. Ensuring minimal vibration and a stable testing setup is crucial to prevent any inadvertent impacts on the indentation process. By maintaining a controlled and consistent testing environment, the reliability and precision of hardness testing can be maximized, allowing for accurate material characterization and quality assurance.
Understanding the interplay between operator skill, sample preparation, and test conditions is crucial for achieving accurate hardness test results. By adhering to rigorous testing protocols and maintaining high standards in these practical aspects, professionals can ensure that the use of the Hardness Tester Scale yields dependable and reproducible data, essential for material selection and quality control in various industrial applications.
Summary of Key Insights on Selecting the Right Method
Overview of Main Points Discussed
In the varied and intricate landscape of hardness testing, each method—Vickers, Rockwell, and Brinell—exhibits unique strengths and challenges. The Vickers Hardness Test stands out for its high precision, particularly suitable for thin materials and coatings due to its small indentation size. However, it requires meticulous sample preparation and skilled operators to ensure accuracy. The Rockwell Hardness Test is praised for its simplicity and rapidity, making it highly effective in production environments where quick, repeatable results are critical. Yet, it can face inconsistencies due to material surface conditions and hardness gradients. The Brinell Hardness Test is ideal for materials with non-uniform or coarse grain structures, providing reliable and reproducible results by averaging out microstructural inconsistencies. However, it is slower and requires precise measurements of larger indentations and careful surface preparation.
Conclusion on Accuracy Among Methods
Accuracy in hardness testing is a multifaceted concept, influenced by the specific Hardness Tester Scale employed, the material’s properties, the operator’s expertise, and the environmental conditions. The Vickers method, with its microscopic precision, generally offers high accuracy for a broad range of materials but mandates a smooth surface and expert handling. The Rockwell method, though less precise on very hard or thin materials, excels in industrial settings where speed and ease are vital. The Brinell method, while slower, provides dependable accuracy for larger, industrial components with coarse structures. Ultimately, no single method can be deemed universally superior; rather, the choice should be guided by the specific application, material properties, and desired balance of speed and precision.
Guidance on Choosing an Appropriate Testing Method
Choosing the correct Hardness Tester Scale necessitates a deep comprehension of the material characteristics and the specific testing needs. Here are some pointers to aid in making a well-informed decision:.
- Consider Material Properties: For hard materials like ceramics and thin coatings, the Vickers test is highly suitable due to its precise microscopic measurements. For metals with consistent surface finishes, the Rockwell test is advantageous, offering quick and repeatable results ideal for production settings. For large, coarse structures such as cast iron, the Brinell test is appropriate, providing reliable results by averaging surface inconsistencies.
- Match the Method to the Application: If rapid testing and minimal sample preparation are priorities, as in high-throughput manufacturing environments, the Rockwell method is suitable. For detailed laboratory analysis where high precision is critical, the Vickers method is preferable. For industrial components where the material’s surface is irregular or coarse, the Brinell method’s tolerance to surface imperfections makes it the best choice.
- Ensure Proper Training and Environmental Controls: The accuracy of any hardness testing method is contingent on operator skill and consistent testing conditions. Ensuring operators are well-trained and the testing environment is controlled—free from contaminants, vibrations, and temperature fluctuations—is paramount for obtaining reliable results.
By thoroughly evaluating these aspects, industry experts can choose the most suitable Hardness Tester Scale tailored to their material and application requirements. This well-informed decision-making process guarantees precise and significant hardness readings, resulting in superior material performance, elevated product quality, and optimized manufacturing procedures.