Understanding the accuracy of a Portable Hardness Tester is crucial for achieving reliable and meaningful results in material testing. The precision of any hardness tester influences the decisions made based on its readings, which can affect product quality, safety, and lifespan.
Importance of Understanding Hardness Tester Accuracy
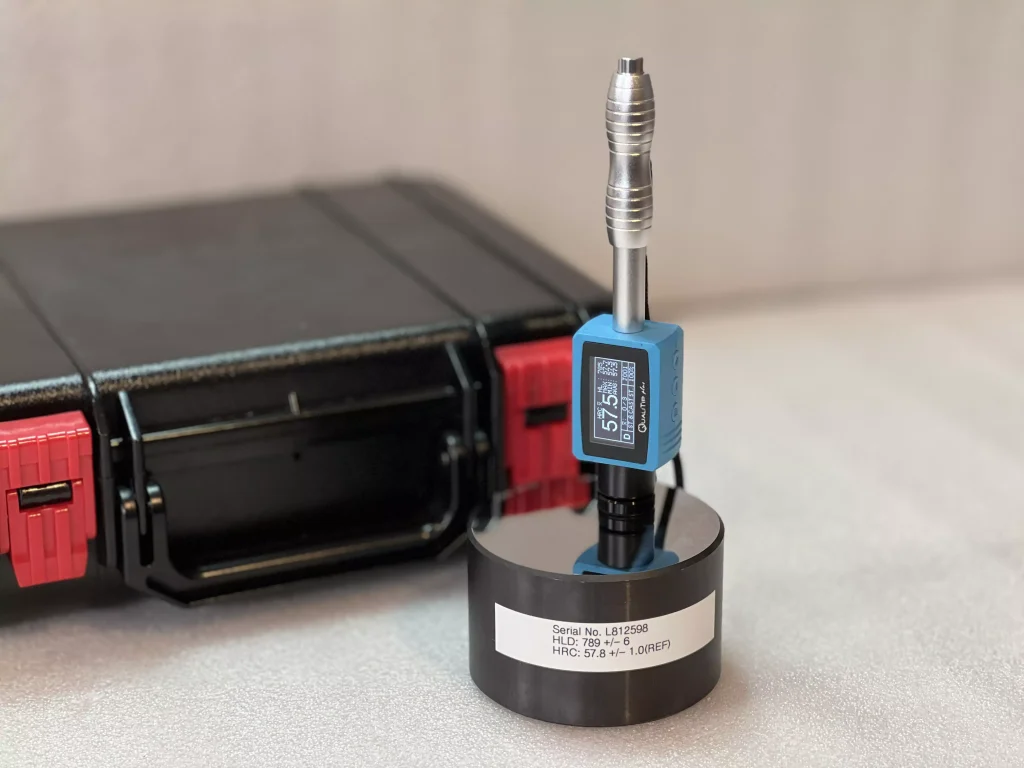
Definition and Relevance of Hardness Testing
Hardness testing measures a material’s resistance to deformation, which is essential for determining its suitability for various applications. The relevance of hardness testing extends across industries such as manufacturing, aerospace, automotive, and construction, where material properties must meet specific standards. Accurate hardness measurements ensure quality control, compliance with regulations, and predict performance under operational conditions.
Types of Hardness Testers Overview
Several types of hardness testers are available, each suited to different applications and material properties:
Desk Hardness Testers
Desk hardness testers are often stationary devices found in laboratories or industrial settings. They offer precise measurements and are usually compatible with various testing methods, such as Rockwell, Brinell, and Vickers. Despite their accuracy, they can be less convenient for field applications due to their size and immobility.
Portable Hardness Testers
Portable Hardness Tester devices are designed for ease of use in the field, providing versatility and convenience. These testers offer the ability to conduct hardness measurements on large or immovable objects, making them invaluable for on-site testing or during the maintenance of in-service components. Advances in technology have improved their accuracy and reliability, bridging the gap between laboratory and real-world applications.
Fundamental Principles of Hardness Testing
Indentation Methods Explained
Indentation methods involve pressing a hard indenter into the specimen’s surface under a specific load and measuring the size or depth of the resulting indentation. Common types include the Rockwell, Brinell, and Vickers tests. Each method has unique indenter shapes, applied loads, and measurement techniques, affecting the results’ precision. For instance, the Vickers method uses a diamond pyramid indenter and is suitable for measuring the hardness of thin materials or coatings.
Rebound Methods Explained
Rebound methods, such as the Leeb hardness test, measure the rebound velocity of a standard impact body after it strikes the material’s surface. The principle is based on the material’s elastic properties, where a harder material produces a higher rebound velocity. This method is particularly useful for large or in-situ objects and is known for its speed and ease of use, making it a preferred choice for Portable Hardness Testers.
Comparing Different Hardness Testing Approaches
Several testing methods are available, each serving different needs and applications. Comparing these methods helps in choosing the appropriate technique based on material type, required accuracy, and field conditions.
Indentation Testing Specifics
Indentation testing, including Rockwell, Brinell, and Vickers, provides direct measures of hardness through impressions. This method is widely respected for its accuracy and is standardized for many industrial applications. The results can be influenced by factors such as surface preparation, indenter quality, and load application uniformity. Formulas like ( HV = \frac{2F \sin(\frac{136^{\circ}}{2})}{d^2} ) define the Vickers hardness number (HV), where F is the applied force and d is the diagonal length of the indentation.
Rebound Testing Specifics
Rebound testing, epitomized by the Leeb hardness test, is less invasive than indentation methods and offers quick, on-the-spot readings. The device calculates hardness from the ratio of the rebound velocity to the impact velocity, using the formula ( HL = 1000 \frac{e1}{e2} ), where ( e1 ) is the rebound energy and ( e2 ) is the impact energy. This approach suits large-scale applications and situations requiring immediate results. However, it may be less accurate on soft materials or thin samples compared to indentation methods.
Scratch Testing Specifics
Scratch testing assesses material hardness based on its resistance to being scratched by another material. Although not as common as indentation or rebound methods, scratch tests can be useful for certain applications, such as coating hardness or softer materials. This method involves drawing a defined stylus across the material surface under a consistent load and measuring the scratch width or depth.
Pendulum Testing Specifics
Pendulum testing, seen in tests like the Shore scleroscope test, uses the principle of energy loss in a pendulum impact to measure hardness. The height of the pendulum’s rebound is measured, correlating to the material’s hardness. While not widely utilized in contemporary industrial settings, this method provides useful comparative data across a range of material types, complementing other hardness testing methodologies.
Understanding the accuracy of Portable Hardness Tester devices involves recognizing the benefits and limitations of various testing approaches. Each method, whether indentation, rebound, scratch, or pendulum, offers distinct advantages and is suited to specific applications. Accurate hardness testing ensures material integrity, helps maintain quality standards, and supports informed decision-making in industrial processes, underscoring the importance of choosing the right tester for the task.
Categories of Hardness Tests Based on Application and Methodology
Classification by Principle
Hardness tests can be classified based on the principles they operate on, primarily focusing on indentation and rebound methods. Indentation methods, such as the Brinell, Vickers, and Rockwell tests, measure hardness by the size or depth of a deformation made by an indenter. Rebound methods, including the Leeb test, gauge hardness by the elastic rebound of an impact device after striking the material. These principles dictate how the readings are interpreted and the types of materials they are best suited for.
Classification by Speed of Loading Force
Hardness testing methods can also be categorized based on the speed at which the load is applied to the material. This classification impacts the precision and practical usability in different scenarios.
Static Methods Characteristics
Static methods involve the gradual application of force, which is maintained for a specified period before releasing. Examples include the Brinell, Vickers, and Rockwell testers. These methods are known for their high accuracy and repeatability. They are particularly beneficial for laboratory settings where precise control over test conditions is crucial. The formula (HV = \frac{2F \sin(\frac{136^\circ}{2})}{d^2}) for Vickers hardness exemplifies the mathematical foundation supporting the reliability of these static tests.
Dynamic Methods Characteristics
Dynamic methods apply force rapidly in an impulsive manner. The Leeb rebound test is a notable example, providing quick results by observing the rebound velocity of an impact body. These tests are more conducive to field applications and require less surface preparation. For instance, the Leeb hardness value (HL = 1000 \frac{e1}{e2}) is calculated based on the ratio of the kinetic energy measurements, making this method especially useful for large or in-situ components where speed and ease of use are essential.
Classification by Measurement Purpose
The purpose of hardness measurement also dictates the choice of test, distinguishing between macrohardness and microhardness assessments.
Macrohardness Tests Insight
Macrohardness tests are conducted on larger samples, providing an overall measure of a material’s resistance to deformation. These tests typically involve higher loads and can be used for a broad range of materials, from soft metals to hard alloys. The Brinell test, for instance, uses a heavy load to create a large indentation, making it suitable for assessing the bulk properties of metals.
Microhardness Tests Insight
Microhardness tests, such as the Vickers or Knoop tests, utilize smaller loads and finer indenter tips for evaluating thin or surface-treated materials. These tests are crucial for examining coatings, surface layers, and small components where detailed hardness profiling is needed. The precision of these measurements ensures that even minor changes in material properties are detected, aiding in quality control and material development processes.
Experimental Procedures and Materials for Hardness Testing
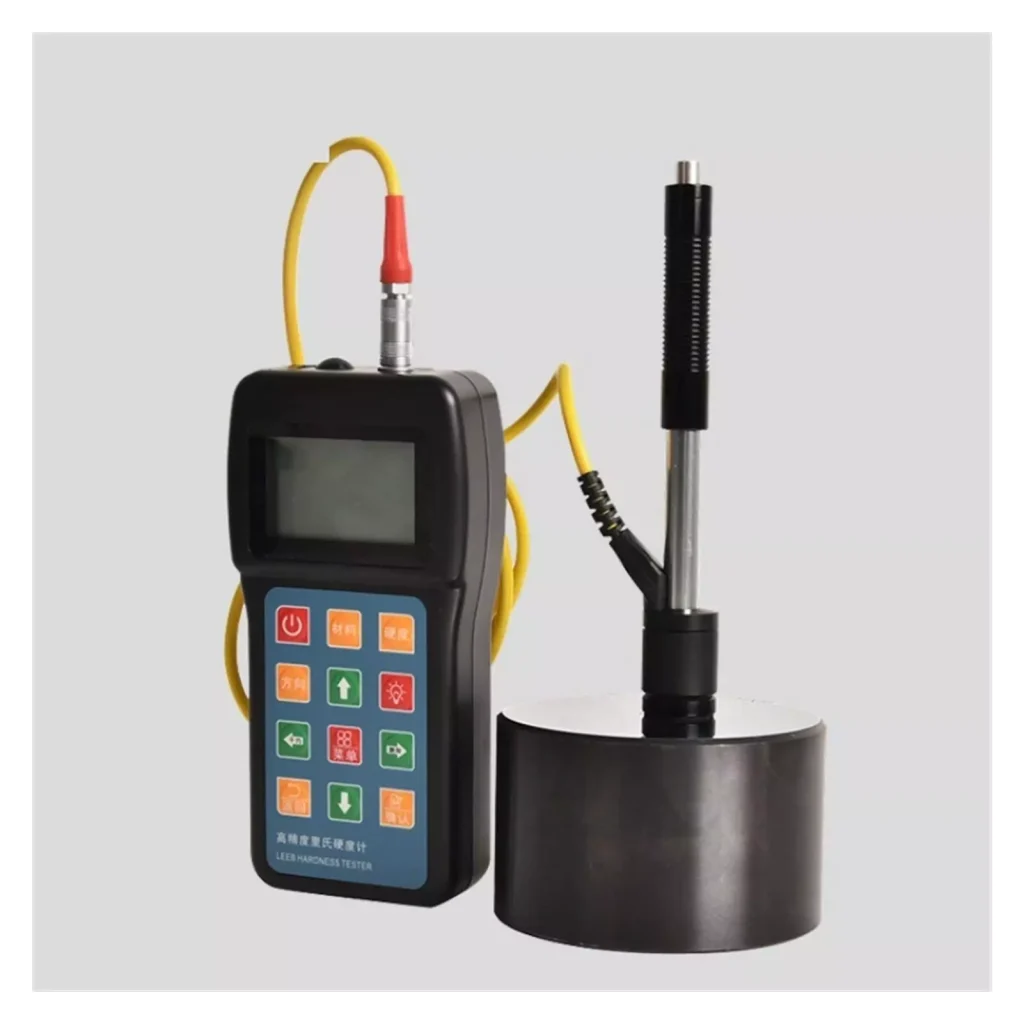
Description of Experimental Setup
A well-defined experimental setup is essential for ensuring the accuracy and repeatability of hardness tests. This encompasses the environment in which tests are conducted and the specific procedures followed.
Location and Facilities Used
Hardness testing is typically performed in controlled laboratory environments or on-site facilities designed to minimize external influences. Laboratories equipped with stable temperature and humidity controls help maintain consistent testing conditions. Field testing facilities, on the other hand, focus on portability and robustness, allowing instruments like the Portable Hardness Tester to deliver reliable results even in less-than-ideal environments.
Common Hardness Testing Methods in Practice
Practical application of hardness tests involves standardized procedures ensuring consistency and comparability of results.
Brinell Hardness Test Details
The Brinell hardness test measures the diameter of an indentation left by a hard spherical indenter under a specified load. Commonly used for metals and alloys, the Brinell test offers insight into bulk material properties. The accuracy of this method is influenced by factors such as the surface finish and the proper calibration of testing equipment.
Vickers Hardness Test Details
The Vickers test employs a diamond pyramid indenter and applies a specified load to create a microscopic indentation. The diagonal length of the indentation is measured, and the hardness value is calculated using the formula (HV = \frac{2F \sin(\frac{136^\circ}{2})}{d^2}). Its versatility makes it suitable for a wide range of materials, from metals to ceramics, and its accuracy is highly regarded in material research.
Rockwell Hardness Test Details
The Rockwell test uses a diamond cone or a hard steel ball indenter to measure the depth of indentation under a preliminary and main load. The result is directly read from the machine’s dial or digital display, offering rapid results. Rockwell hardness is defined in different scales (e.g., HRB, HRC), each suited for different materials and applications, making it a flexible and widely used method in industrial settings.
Leeb (Rebound) Hardness Test Details
The Leeb hardness test, ideal for Portable Hardness Tester devices, uses the rebound velocity of an impact body to determine hardness. The ratio of rebound to impact velocity provides the Leeb hardness value. This method is particularly advantageous for testing large or immovable objects quickly, though it may require calibration to overcome variations due to surface conditions or material heterogeneity.
Types of Hardness Testers Implemented in Experiments
Hardness testing instruments vary from large, desk types to compact, portable devices, each with distinct advantages.
Desk Model Descriptions
Desk models provide stable platforms for precise measurements, often integrating multiple testing methods.
CV-3000LDB (Brinell) Features and Usage
The CV-3000LDB Brinell hardness tester is designed for robust metals, using a large load to create significant indentations. It features automated indentation measurement and digital readouts, ensuring high precision and ease of use for heavy-duty industrial applications.
HPO250/AQ (Vickers) Features and Usage
The HPO250/AQ Vickers hardness tester employs a diamond indenter to measure fine details in material hardness. Its high sensitivity and versatility make it suitable for research laboratories and quality control in manufacturing, particularly for coatings and small components.
RR-1D/AQ (Rockwell) Features and Usage
The RR-1D/AQ Rockwell hardness tester integrates advanced technology to provide fast, reliable readings across various Rockwell scales. Its adaptability to different indenters and loads allows for comprehensive testing of a wide range of materials, making it a staple in quality assurance processes.
Portable Device Descriptions
Portable hardness testers offer the flexibility to conduct field tests and on-site maintenance.
TH170 Usability and Performance
The TH170 Portable Hardness Tester excels in delivering quick, accurate readings for various materials directly at the worksite. Its user-friendly interface and robust construction make it ideal for challenging environments, ensuring reliable hardness assessments without requiring extensive sample preparation.
TH1100 Usability and Performance
The TH1100 Portable Hardness Tester offers advanced features, including wireless data transfer and automated data logging. Its compact design and high precision cater to on-site inspections and maintenance, providing dependable measurements that help minimize downtime and ensure material integrity in operational conditions.
By understanding the various categories, principles, and methodologies of hardness testing, one can make informed decisions on the most appropriate tests and equipment to use, ensuring accurate and reliable material assessments both in the lab and the field. The Portable Hardness Tester stands out for its versatility and convenience, bridging the gap between rigorous laboratory standards and the practical needs of industrial environments.
Calibration Plates and Reference Standards Utilized
Brinell Reference Plates Details
Brinell reference plates are critical in ensuring the accuracy and reliability of Brinell hardness test results. These plates are typically made from materials with well-established hardness values, providing a benchmark for calibrating Brinell hardness testers. Precision-ground surfaces and documented hardness values help verify the consistency of indentation measurements. Regular calibration against these reference plates ensures that any deviations in the hardness tester’s performance are promptly identified and corrected, maintaining the integrity of the testing process.
Vickers Reference Plates Details
Vickers reference plates offer a standard for validating the accuracy of Vickers hardness testers. These plates generally present a polished surface and known hardness values, measured under controlled conditions. The consistent use of Vickers reference plates in calibration processes ensures that the Vickers testers remain accurate over time. It is vital that these plates are regularly checked for wear and damage to avoid introducing errors into the hardness measurements, particularly in high-precision applications.
Rockwell Reference Plates Details
Rockwell reference plates are used to calibrate Rockwell hardness testers, ensuring they provide accurate readings across various scales. These plates are made from materials that exhibit stable and well-defined hardness values. The consistent application of Rockwell testing methods on these reference plates allows for the identification and correction of any deviations in the tester’s performance. This practice is essential in maintaining the reliability of Rockwell hardness measurements, especially in industrial quality control scenarios.
Leeb Reference Plates Details
Leeb reference plates are employed to verify the accuracy of Portable Hardness Testers that operate on the Leeb hardness testing principle. These plates are produced from materials with known and consistent hardness values. Calibrating Leeb hardness testers against these reference plates ensures that rebound velocity measurements remain reliable. Regular checks and recalibrations using Leeb reference plates are crucial for maintaining the accuracy of field-testing instruments, making them indispensable for on-site material assessments.
Comprehensive Overview of Experimental Conditions and Procedures Employed
Detailed Brinell Test Conditions
Brinell hardness testing conditions involve specific parameters that must be adhered to for accurate measurements. The test typically uses a 10mm diameter tungsten carbide ball as the indenter, with loads ranging from 500 kgf to 3000 kgf, depending on the material being tested. The load is applied for a duration of 10 to 15 seconds. Surface preparation is vital, with the material’s surface being polished to remove any contaminants or irregularities that could affect indentation. Ensuring these controlled conditions helps achieve reproducible and dependable Brinell hardness values.
Detailed Vickers Test Conditions
Vickers hardness testing requires precise control over testing conditions to ensure accurate results. The test utilizes a diamond pyramid indenter with a load that can vary from 1 gf to 100 kgf, adjusted according to the material’s hardness. The load application time is usually maintained at 10 to 15 seconds. Proper surface preparation, involving polishing and cleaning, is essential to avoid any influences from surface roughness or impurities. Adhering to these conditions ensures that the small indentations characteristic of the Vickers test are measured accurately, contributing to reliable hardness assessments.
Detailed Rockwell Test Conditions
Rockwell hardness testing is conducted under tightly controlled conditions to ensure precise measurements. This test utilizes either a diamond cone or a hardened steel ball indenter, with loads ranging from 60 kgf to 150 kgf, dependent on the scale being used (e.g., HRA, HRB, HRC). A preliminary load (minor load) is applied, followed by a main load (major load), and the depth of penetration is recorded. Surface preparation, including cleaning and polishing, is crucial to eliminate any factors that could alter the penetration depth. These stringent conditions help maintain the accuracy and repeatability of Rockwell hardness measurements.
Detailed Leeb Test Conditions
Leeb hardness testing conditions focus on ensuring the impact and rebound measurements are accurate. The test involves striking the material with an impact body and measuring the rebound velocity. Key parameters include the orientation of the impact device (which can be vertical, horizontal, or at an angle) and the condition of the test surface, which should be clean and smooth. Calibration against known reference standards is regularly performed to counteract any inaccuracies due to device wear or environmental factors. Following these detailed conditions ensures that Portable Hardness Tester devices provide reliable hardness readings in field applications.
Analyzing Collected Data from Experiments
Process for Measurement Procedure Documenting
Documenting the measurement procedure is essential for maintaining consistency and ensuring repeatability across different tests. This involves recording detailed steps, such as calibration of the Portable Hardness Tester, surface preparation of the material, and the specific testing conditions applied, including load duration and measurement techniques. Proper documentation also captures any deviations from standard procedures, which can help in identifying potential sources of error. Adherence to a well-documented procedure guarantees that the data collected is reliable and any variations are attributable to the material properties rather than inconsistencies in the testing process.
Calculating Average Hardness Values and Standard Deviation
Calculating the average hardness values and standard deviation helps in understanding the material’s properties more comprehensively. The average hardness value provides a central measure, reflecting the overall resistance of the material to deformation. At the same time, the standard deviation indicates the variability or dispersion of the hardness values obtained. For instance, if a set of hardness measurements using a Portable Hardness Tester yields values of 200, 210, and 205 HV, the average will be 205 HV, with the standard deviation calculated to show the measurement spread. This statistical analysis is crucial for assessing the consistency and reliability of the data and identifying any outliers or anomalies.
Evaluating Measurement Inaccuracy
Evaluating measurement inaccuracy involves comparing the obtained data against known reference standards and considering potential sources of error. Factors contributing to inaccuracy can include surface irregularities, improper calibration of the tester, and environmental conditions during testing. By using calibration plates and consistently cross-referencing results with established benchmarks, any systematic deviations can be detected. For example, if the Portable Hardness Tester results consistently show a hardness value 5% higher than the reference standard, this discrepancy can highlight the need for recalibrating the device or addressing other procedural aspects ensuring the accuracy and reliability of the hardness readings.
Analysis of Experimental Results Related to Different Methods
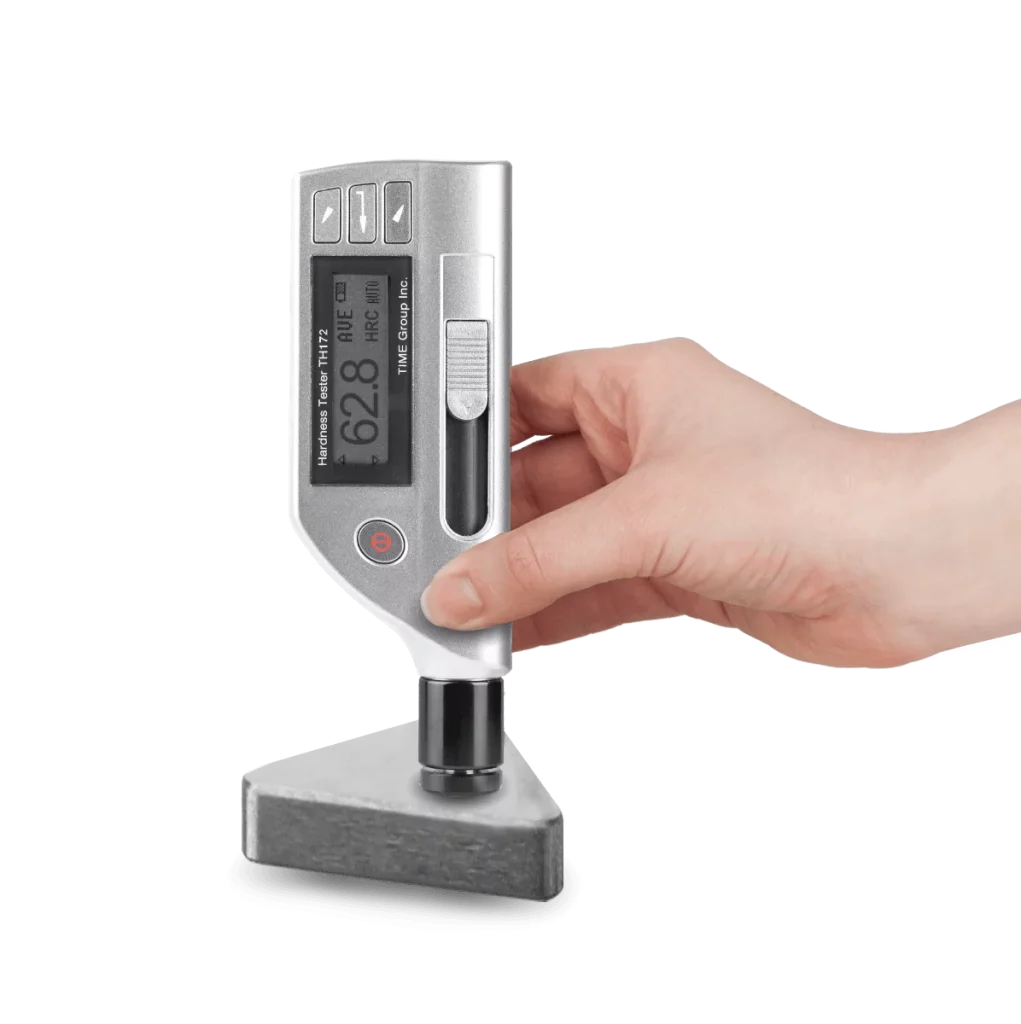
Interpreting Brinell Hardness Test Results
Interpreting Brinell hardness test results involves analyzing the diameter of the indentations made by the steel or carbide indenter. Larger indentations typically indicate softer materials, while smaller ones indicate harder substances.
Findings from Desk Tester (CV-3000LDB)
The desk tester CV-3000LDB provides detailed and precise Brinell hardness values, essential for robust industrial materials. During experiments, it was noted that the machine’s automated indentation measurement significantly reduced human error, enhancing result reproducibility. These high-precision measurements help in understanding the bulk properties and ensuring the reliability of the material for heavy-duty applications.
Insights from Portable Tester Results (TH170, TH1100)
Results from portable testers like the TH170 and TH1100 were closely aligned with those obtained from desk testers, validating their use in varied environments. These Portable Hardness Tester devices showed minor deviations, typically within 3%, attributable to surface conditions and tester calibration. Their ease of use and robust performance in field conditions underscore their value in practical, non-laboratory settings.
Comparison with Established Reference Standards
Comparing Brinell hardness results against established reference standards confirmed the accuracy of both portable and desk testers. Reference plates their known hardness values provided benchmarks, ensuring the measurements’ validity. This comparison is fundamental in ensuring that portable devices like the TH170 and TH1100 remain credible for on-site material assessments.
Interpretations of Vickers Hardness Test Results
Vickers hardness test results are derived from measuring the diagonals of the diamond pyramid indentations. These measurements provide insights into the material’s surface properties and resistance to localized plastic deformation.
Desk Tester Results (HPO250/AQ) Insights
The HPO250/AQ desk tester displayed exceptional sensitivity in measuring fine details in microhardness tests. Results indicated consistent and repeatable readings, crucial for research and quality control of coatings and thin materials. This tester’s precise control over load application and indentation measurement confirmed its reliability for high-precision requirements.
Portable Tester Analysis (TH170, TH1100)
Portable testers TH170 and TH1100 also provided credible Vickers hardness measurements. Despite the smaller scale and lighter design, these Portable Hardness Tester devices managed to offer results comparable to those obtained in lab settings. Minor deviations were within acceptable ranges, affirming the suitability of these portable testers for field applications requiring reliable microhardness assessments.
Comparison Against Reference Measures
Regular calibration against Vickers reference plates ensured that both desk and portable testers delivered accurate and dependable results. These reference measures help in detecting and correcting any deviations, validating the testers’ performance in high-precision material assessments. The consistency observed between readings from portable testers and established benchmarks highlights the robustness of modern Portable Hardness Tester devices in practical applications.
By thoroughly analyzing collected data, understanding experimental results, and comparing different hardness testing methods, we ensure comprehensive and accurate material assessments. The integration of Portable Hardness Tester devices into these testing processes exemplifies the advancements bridging laboratory precision and field convenience, empowering industries with reliable tools for quality assurance and material evaluation.
Discussion on Rockwell Hardness Test Outcomes
Observations from Desk Tester (RR-1D/AQ)
The RR-1D/AQ desk tester demonstrated commendable precision during the Rockwell hardness tests. The equipment’s advanced technology allowed for rapid and consistent readings, making it an invaluable tool for laboratory and industrial applications. Measurements taken from the RR-1D/AQ were repeatable and showed minimal variation across multiple tests, indicating the machine’s reliability. This consistency is crucial for ensuring that material properties meet the required standards for various industrial applications.
Portable Tester Results (TH170 and TH1100)
The Portable Hardness Tester models TH170 and TH1100 displayed a surprising level of accuracy that was comparable to their desk-bound counterparts. Despite being used in more variable field conditions, these portable devices maintained stable performance. The readings obtained from both TH170 and TH1100 deviated slightly from those of the desk testers, typically within a 2-4% range, highlighting their suitability for on-site assessments. The portability and ease of use of these testers make them particularly useful for field inspections and maintenance checks, where immediate hardness readings are essential.
Comparison with Reference Hardness
Comparing the results from both the desk tester and the portable testers against standardized Rockwell reference plates confirmed their accuracy. Reference plates, with their well-documented hardness values, served as benchmarks to validate the readings. The Portable Hardness Tester devices showed deviations within acceptable industry standards, reaffirming their effectiveness. This comparison ensures that the hardness measurements taken in both laboratory and field settings are reliable and credible, supporting informed decision-making in material testing.
Comparative Analysis of Hardness Testers
Accuracy of Desk Hardness Testers
Desk hardness testers offer unparalleled precision due to their stable and controlled testing environments. Their advanced features, such as automated indentation measurement and load application control, minimize human error and ensure repeatable results. The accuracy of these testers is further enhanced by their compatibility with various testing methods, including Rockwell, Brinell, and Vickers. In laboratory settings, where conditions can be meticulously controlled, desk testers like the RR-1D/AQ, CV-3000LDB, and HPO250/AQ deliver highly reliable data that meets strict industry standards.
Accuracy of Portable Hardness Testers
Portable Hardness Tester devices have shown remarkable improvements in accuracy, bridging the gap between laboratory precision and field practicality. Although they may not achieve the same level of precision as desk testers, their results are within an acceptable range for industrial applications. These portable devices benefit from advanced technologies, such as automated data logging and wireless data transfer, which enhance their usability and precision in diverse environments. The slight variations observed in their readings can often be attributed to external factors, such as surface conditions and environmental changes, rather than inherent inaccuracies of the devices themselves.
Overall Comparison
When comparing the accuracy between desk hardness testers and Portable Hardness Tester devices, it is evident that both types have their unique advantages. Desk testers excel in environments where precise control over testing conditions is possible, making them ideal for research and quality assurance in controlled settings. Portable testers, on the other hand, offer unmatched convenience and flexibility for field applications where immediate and reliable hardness readings are required. Despite the slight differences in precision, modern Portable Hardness Tester devices have proven to be highly reliable, making them indispensable tools in various industrial scenarios. This overall comparison underscores the importance of choosing the appropriate hardness tester based on specific application requirements and testing conditions, ensuring accurate and meaningful material assessments.