What Are Carbide Inserts?
Definition and Function
Carbide inserts, crucial components in the machining and metalworking industries, are sophisticated cutting tools used in a variety of machining operations. These inserts are designed to be replaceable, making them a cost-effective and efficient choice for manufacturers. Carbide inserts are typically mounted onto a tool holder, and they excel at cutting, grooving, milling, and threading various materials. The replaceable nature of these inserts significantly reduces downtime and enhances productivity in machining processes.
Materials Used
Carbide inserts are renowned for their versatility in machining different materials. They are especially efficient when working with:
- Cast Iron: Offering optimal hardness, carbide inserts perform exceptionally well in machining cast iron, delivering clean and precise cuts.
- Steel: The inserts can withstand high temperatures and maintain their cutting efficiency when machining steel, making them indispensable for automotive and heavy machinery manufacturing.
- Carbon and Non-Ferrous Metals: Carbide inserts excel in cutting both carbon steels and non-ferrous metals such as aluminum and copper, ensuring good surface finishes and extended tool life.
- High Melting Point Alloys: Dealing with materials such as titanium and nickel-based superalloys, carbide inserts ensure that operations are carried out with maximum efficiency and minimal tool wear.
Advantages
The use of carbide inserts offers numerous advantages that make them a preferred choice in the machining industry:
- High-Speed Machining: Carbide inserts are capable of operating at higher speeds, which translates into reduced machining time and increased productivity.
- Better Surface Finishes: These inserts provide superior surface finishes due to their precision and sharp cutting edges, reducing the need for additional finishing operations.
- Efficiency in Material Removal: Carbide inserts are designed for efficient material removal, which is crucial for high-volume production environments where speed and efficiency are paramount.
Types of Carbide Inserts
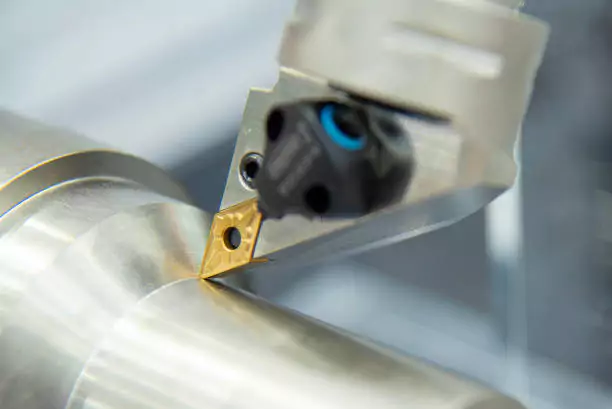
Turning Inserts
Turning inserts are used predominantly in lathe operations to remove material from a rotating workpiece. They are designed to withstand the stresses of cutting and provide durability and efficiency. Made from a combination of carbide and various coatings, they can handle different types of materials while delivering precise results.
Threading Inserts
Threading inserts are specialized tools used to create internal and external threads. They attach to tool holders and are engineered to produce threads with high accuracy and consistency. The versatility of threading inserts allows them to be used for a wide range of pitches and thread sizes, making them essential for producing threaded components in the manufacturing industry.
Grooving Inserts
Grooving inserts come into play for both external and internal grooving applications. These inserts are used to cut grooves or channels into the workpiece. Different types of grooving tools cater to various grooving needs, whether it be parting-off, face grooving, or specialized grooving for specific applications. The precision and reliability of these inserts ensure that grooves are machined to exact specifications.
Milling Inserts
Milling inserts are highly versatile tools used in milling operations to shape and process materials. They are designed to handle robust applications and can machine various materials ranging from steel to aluminum. Milling inserts contribute to the effectiveness and efficiency of milling operations, offering clean finishes and extended tool life due to their durable construction.
Drilling Inserts
Designed for drilling operations, carbide inserts enhance the accuracy and performance of the drilling process. Their material compatibility allows them to be used with different types of workpieces, and their precision ensures that holes are consistent and meet exact specifications. The use of drilling inserts leads to reduced tool changes and increased operational efficiency.
Boring Inserts
Boring inserts are tailored for metal machining operations that require the enlargement of existing holes. These inserts come in varied sizes, shapes, and compositions to suit different machining requirements. They offer high efficiency and accuracy, making them essential for applications where precise hole dimensions and smooth finishes are critical.
Identifying Carbide Inserts Using Codes
ISO Code System
Purpose and Benefits
The ISO code system for carbide inserts provides a standardized method for identifying and categorizing inserts based on their shape, size, and other characteristics. This system simplifies the selection process and ensures compatibility across different tools and machines. The standardized codes enhance communication and understanding among manufacturers and end users, promoting efficiency and accuracy in machining operations.
Shape Identification
Standard Insert Shapes
Identifying the shape of a carbide insert is crucial for ensuring it fits the intended tool holder and meets the machining requirements. Standard insert shapes include:
- Parallelogram: Suitable for finishing applications, parallelogram inserts offer balanced cutting performance and versatility.
- Diamond (Rhombic): Commonly used in turning operations, diamond inserts provide smooth finishes and are ideal for precision applications.
- Hexagon: Hexagon inserts combine robustness and reliability, making them suitable for both heavy and light cutting operations.
- Rectangle: These inserts are often used in grooving and parting operations, where stability and accuracy are critical.
- Octagon: Known for their multiple cutting edges, octagon inserts are preferred for extended tool life and efficient material removal.
- Pentagon: Unique to specific applications, pentagon inserts deliver reliable performance while providing flexibility in machining.
- Round: Round inserts are versatile and can handle a variety of cutting tasks, offering continuous edge usage and reducing downtime.
- Square: They are preferred for their durability and ability to handle robust machining tasks without compromising on accuracy.
- Triangle: Triangle inserts are ideal for precision cutting and are commonly used in turning operations due to their versatility.
- Trigon: These inserts are designed to balance the need for strength and precision, making them suitable for a range of cutting applications.
Clearance Angles
Clearance angles in carbide inserts play a vital role in ensuring effective cutting performance and tool longevity. Standard relief angles, measured in degrees, determine the clearance between the cutting edge and the workpiece. Proper clearance angles reduce friction and prevent the insert from overheating and wearing out prematurely. Incorrect relief angles may lead to poor surface finishes and increased resistance during the cutting process.
Tolerance Classes
Tolerance classes are crucial for controlling the indexability and precision of carbide inserts. Various tolerance indicators denote the permissible variations in dimensions and shape, ensuring that each insert meets stringent quality standards. Adhering to these tolerance classes is essential to maintain consistent machining results and prolonged tool life. Tolerance letters and grades help machinists quickly identify the acceptable range of deviation, reducing potential errors and ensuring reliable performance.
Insert Types
Carbide inserts come with specific features such as fixing holes and countersinks, which enhance their attachment to tool holders. Additionally, special rake surface features are designed to improve chip flow and reduce cutting resistance, resulting in smoother machining operations and improved surface finishes. Inserts with unique rakes or special cutting edges are tailored to specific applications, enabling efficient material removal and enhanced performance in specialized tasks.
Size Indicators
Understanding the size indicators for carbide inserts, such as the inscribed circle diameter and rectangular or parallelogram dimensions, is essential for selecting the appropriate insert for specific applications. These dimensions ensure that the insert fits correctly in the tool holder and provides optimal cutting performance. Accurate size selection minimizes tool change time and enhances overall machining efficiency, leading to better consistency and quality in the finished products.
Thickness Measurements
Thickness measurements of carbide inserts are vital to ensuring the insert’s robustness and ability to endure the stresses of cutting operations. Thickness indicators, often listed in millimeters, help in determining the insert’s load-bearing capacity and resistance to breakage. Precision in thickness ensures stability during high-speed machining and reduces the chances of insert failure, contributing to better productivity and safety in the machining process.
Cutting-Point Configuration
The cutting-point configuration, including radius and facet indicators, plays a significant role in the effectiveness of the carbide insert. Radius indicators determine the nose radius of the insert, influencing the surface finish and cutting forces. Smaller radii are suitable for fine finishing, while larger radii are ideal for roughing applications. Facet indicators specify additional features that enhance chip control and cutting efficiency, ensuring optimal performance for specific machining tasks.
Edge Preparation
Edge preparation techniques for carbide inserts, such as hone, radius, and chamfer, are crucial for ensuring the durability and cutting efficiency of the insert. Edge treatments can significantly impact wear resistance and cutting performance. Proper surface finish descriptions ensure that the insert can handle different materials without chipping or breaking, resulting in longer tool life and consistent machining results.
Hand of Insert
The hand of the insert – right hand, left hand, or neutral – determines the direction of the cutting forces and the suitability of the insert for specific operations. Right-hand inserts are used for clockwise operations, while left-hand inserts are suitable for counterclockwise directions. Neutral inserts provide flexibility, suiting both directions. Correctly identifying the hand of the insert ensures optimal alignment and effective cutting performance.
Facet Size
Facet size, indicated by nominal measurement indicators, determines the overall geometry and suitability of the insert for various cutting demands. Correct facet size selection ensures smooth material removal and efficient cutting operations. Detailed facet indicators help machinists match the insert to the specific requirements of each task, promoting precision and consistency across different machining applications.
Choosing the Right Carbide Insert
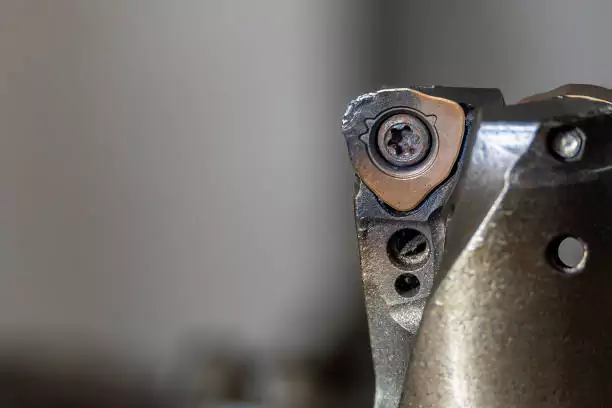
Insert Geometry
The right insert geometry is vital for optimizing cutting performance. Inserts designed for roughing have a stronger edge and larger nose radius to handle bulk material removal. Those for medium processes strike a balance between roughing and finishing, providing moderate edge strength and sharpness. Finishing inserts, with their finer edges and reduced nose radii, ensure superior surface quality, precision, and minimal material distortion. Selecting the appropriate insert geometry aligns cutting operations with desired outcomes, enhancing productivity.
Grade of Carbide Insert
The grade of the carbide insert determines its hardness, toughness, and wear resistance. Different grades are formulated to suit varying machine conditions and materials. For example, harder grades withstand higher temperatures and are suitable for high-speed machining, while tougher grades resist chipping and are excellent for interrupted cuts. Understanding the material composition and manufacturing method of the insert aids in choosing the right grade for the specific machining environment.
Shape of Carbide Insert
The shape of the carbide insert is integral to its performance in different cutting scenarios. Inserts with smaller nose angles are ideal for detailed and accurate cuts, commonly used in finishing processes. Conversely, larger nose angles are suited for heavy cuts and bulk material removal. Balancing the cuts and resources involves selecting the shape that aligns with the machining operation’s specific needs, ensuring efficiency and precision.
Insert Size
The size of the carbide insert affects its compatibility with the tool holder and the depth of cut it can perform. Larger inserts are typically used for deeper and more aggressive cuts, providing stability and durability. Smaller inserts, on the other hand, are perfect for fine, detailed work requiring precision. Considering machining requirements and the tool holder’s specifications is crucial for selecting the right insert size, which directly impacts the machining process’s efficiency and outcome.
Machined Material
Material compatibility is critical when choosing a carbide insert. Different inserts are designed to handle specific materials, such as steel, cast iron, aluminum, or superalloys. Inserts must have the appropriate material composition and edge preparation to resist wear and deliver a smooth cutting performance. Evaluating the machined material’s properties, such as hardness, abrasiveness, and thermal conductivity, ensures the selected insert will meet the machining demands effectively.
Machine Tool Type
The type of machine tool used in the operation influences the choice of carbide insert. Common machines include CNC lathes, milling machines, and drilling machines, each requiring specific insert types to optimize performance. Properly matching the insert to the machine tool enhances cutting efficiency, reduces tool wear, and achieves better-machined part quality. Understanding the machine’s capabilities and limitations helps in selecting inserts that deliver consistent and reliable results.
Carbide vs. Ceramic Inserts
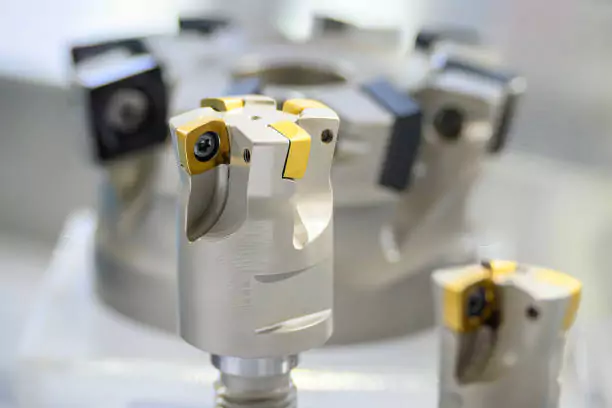
Heat Resistance
Carbide inserts are known for their excellent heat resistance, making them suitable for high-speed machining operations where temperatures can soar. This resistance to heat allows carbide inserts to maintain their cutting edge without deformation, ensuring a consistent and reliable performance. Conversely, ceramic inserts offer even higher heat resistance, often used in applications with extreme heat where carbide would fail. However, ceramic’s brittleness can be a limitation in interrupted cuts.
Longevity
The longevity of carbides and ceramic inserts varies based on their application and the materials they machine. Carbide inserts generally provide a balanced lifespan, excelling in varied conditions with predictable wear patterns. However, ceramics can outlast carbide in high-temperature applications due to their superior heat stability. Proper usage and adherence to recommended parameters significantly extend the working life of both types of inserts.
Durability
Durability is a key factor in choosing between carbide and ceramic inserts. Carbide inserts offer resilience and toughness, capable of handling tough materials and heavy cuts without chipping or breaking easily. Ceramic inserts, while offering excellent wear resistance and heat stability, can be more brittle and prone to cracking under aggressive conditions or interrupted cuts. Understanding the machining environment and requirements is essential in selecting an insert that will withstand the operational demands.
Cost
The cost of carbide inserts is relatively affordable, offering a balance of performance and expense, making them a popular choice in various machining applications. Ceramic inserts tend to be more expensive due to their specialized properties and manufacturing process. Evaluating the cost-effectiveness involves considering the operational benefits and the insert’s longevity against its price, ensuring the best value for the specific machining task.
Coatings
Coatings applied to carbide inserts can significantly enhance their performance by improving wear resistance, reducing friction, and increasing heat dissipation. Common coatings include TiN (titanium nitride), TiAlN (titanium aluminum nitride), and DLC (diamond-like carbon). These coatings extend the insert’s life and improve cutting efficiency. Ceramic inserts usually do not require coatings due to their inherent properties but are sometimes engineered to provide specific surface characteristics for enhanced performance.
Performance
The overall performance of carbide and ceramic inserts is determined by their ability to maintain a sharp cutting edge, resist wear, and deliver desired surface finishes. Carbide inserts are versatile, performing well across a range of materials and machining conditions. Ceramic inserts excel in high-speed, high-temperature applications, providing superior wear resistance and minimal built-up edge. The choice between the two depends on matching the insert’s strengths with the operational requirements, ensuring optimal machining efficiency and quality.
By understanding these aspects, manufacturers can avoid common mistakes in identifying and selecting carbide inserts, ensuring their operations are efficient, productive, and yield high-quality results.